- Bina Rumah Batu-Bata
- Zero Deposit
- Spesifikasi Rumah
- Lokasi Projek
- Pembiayaan LPPSA
- Garis Panduan LPPSA (Rasmi)
- Soalan Lazim LPPSA
- E-Book LPPSA (Download)
- 1. Apa itu LPPSA?
- 2. Kelebihan LPPSA
- 3. Syarat Kelayakan
- 4. Jenis-Jenis Pembiayaan
- Jenis 1 – Pembelian Rumah Kediaman Yang Telah Siap
- Jenis 2 – Membina Rumah Di Atas Tanah Sendiri
- Jenis 3 – Membeli Rumah Kediaman Yang Sedang Dibina
- Jenis 4 – Pembelian Tanah Bagi Pembinaan Rumah
- Jenis 5 – Melunaskan Keseluruhan/ Sebahagian Pinjaman Sedia Ada Daripada Bank/ Institusi Kewangan
- Jenis 6 – Pembinaan Rumah Kediaman Di Atas Tanah Yang Sedang Dibiayai Oleh BPP/ LPPSA
- Jenis 7 – Ubah Suai Rumah Yang Sedang Atau Telah Selesai Bayar Melalui LPPSA
- 5. Semak Kelayakan LPPSA
- 6. Dokumen Yang Diperlukan
- 7. Insurans/ Takaful LPPSA
- 8. Kos Yuran Guaman
- 9. BONUS: Bina Rumah
- Pembiayaan Koperasi
- Pengeluaran KWSP
- Bayaran Tunai
- Kalkulator
Are Prefabricated Houses the Smart Choice? Pros and Cons
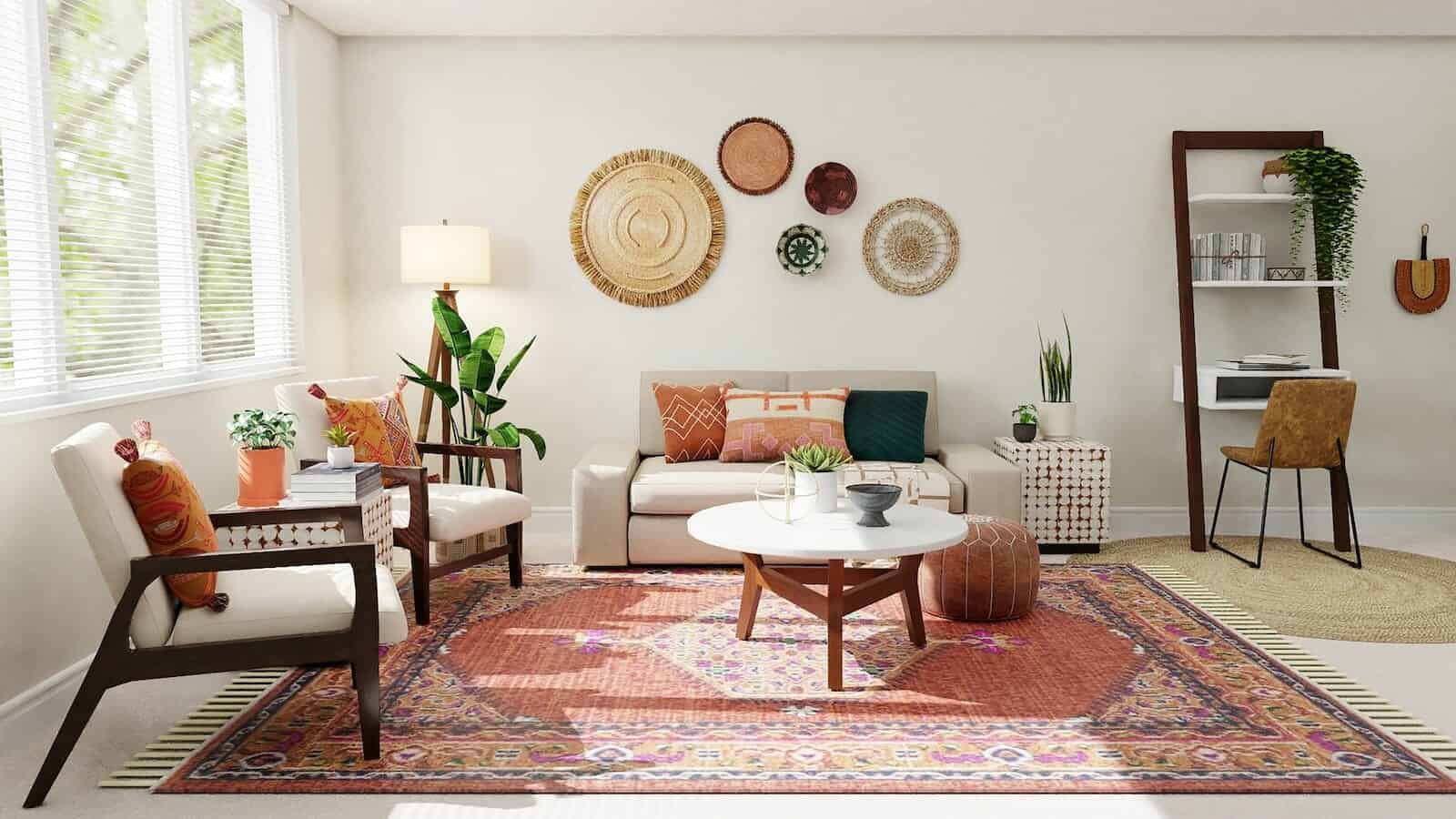
Are Prefabricated Houses the Smart Choice? Pros and Cons
- What are the pros of prefabricated homes?
- What are the cons of prefabricated homes?
- Are prefabricated homes cheaper than traditional construction?
- How long does it take to build a prefab home?
- Are prefabricated homes customizable?
- Do prefab homes appreciate in value like traditional homes?
- Are prefabricated homes energy efficient?
- How durable and long-lasting are prefab homes compared to traditional homes?
- What maintenance is required for prefabricated homes?
- What are the different types of prefabricated homes?
What are the pros of prefabricated homes?
Prefabricated homes, also known as prefab homes, offer many advantages compared to homes built using traditional construction methods. Here are some of the main pros of choosing a prefabricated home:
Faster Construction Time
One of the biggest benefits of prefab homes is the speed of construction. Since up to 80% of a prefab home is built in a factory, construction can be completed much faster than sticking-built homes. Sections of the home are manufactured offsite while the foundation is prepared onsite. Once the foundation is ready, the prefab sections are delivered and assembled. This cuts down on construction time considerably.
- Prefab homes can be move-in ready in as little as 4-5 months, compared to 9-12 months or longer for traditional construction.
Cost Savings
Prefab homes are usually less expensive to build than comparable traditionally-built homes for several reasons:
- Factory construction with assembly line techniques is more efficient. This brings down costs.
- Materials are bought in bulk by the manufacturer, bringing down per unit costs.
- Less on-site labor is required, reducing labor costs.
- Prefab homes produce less waste since materials are precisely manufactured offsite.
According to Consumer Reports, prefab homes cost 10-20% less than traditional construction.
High Quality Construction
Prefab homes are constructed in a controlled factory environment. This allows for:
- Tighter quality control and less defects
- Use of cutting edge technology like CNC machines for precision manufacturing
- Testing and inspection at each step of the construction process
As a result, prefab homes often have higher build quality than site-built homes. Materials and finishes are also not exposed to weather elements during construction.
Customization Options
While there are ready-made standardized prefab designs, many prefab companies also offer customization options:
- Custom layouts and floor plans
- Choice of exterior and interior finishing like siding, roofing, countertops etc.
- Upgrades like solar panels, smart home tech, high-end appliances etc.
So you can still get a customized prefab home tailored to your needs and preferences. The customization takes place at the factory before final delivery and assembly.
Energy Efficiency
Prefab homes are designed for maximum energy efficiency in several ways:
- Wall systems with high insulation ratings to prevent heat loss
- Advanced weather sealing throughout the home
- Energy efficient windows and doors
- Options like solar panels and heat pumps
This results in lower monthly utility bills compared to traditional homes. Some prefab builders even offer net-zero energy homes.
Minimal Site Disturbance
Less on-site construction means:
- Less environmental impact on the building site
- Minimal disruption to the surrounding area
- Reduced noise, debris and pollution during construction
This allows prefab homes to be built on sites like challenging terrains where traditional construction may not even be feasible.
Resilient Design
Prefab construction allows homes to be designed and built to be resilient against disasters like earthquakes, hurricanes and floods. Features include:
- Reinforced roof ties
- Impact resistant windows
- Elevated foundations in flood zones
- Resilient drainage and ventilation systems
This provides security and peace of mind for homeowners.
In summary, prefabricated homes provide faster construction, cost savings, high quality, customization, energy efficiency, sustainability and resilient designs. These pros make them a smart choice compared to conventional construction for many homeowners today.
What are the cons of prefabricated homes?
While prefabricated (prefab) homes have many benefits, there are also some potential drawbacks to consider before choosing a prefab home:
Limited Customization
Prefab homes are not as customizable as homes built completely onsite from the ground up. There are limits to what can be done in the factory manufacturing process. For instance:
- Layout changes may be restricted once manufacturing begins
- Complex custom designs can be difficult to accommodate
- Options for finishes and features are limited to what the manufacturer offers
So for buyers wanting a highly customized or ornate home, prefab may not meet their needs.
Limited Design Options
Currently, there are fewer style options available in prefab home designs compared to traditional construction. Prefab homes tend to have a more modern, minimalist aesthetic. Home buyers preferring traditional architectural styles may not find suitable prefab home designs.
Size Limitations
Prefab homes work best for smaller, compact home footprints. It can be challenging to manufacture, transport and install large prefab sections for sprawling homes over 3,500+ sq.ft. Some local regulations also limit the maximum size of prefab homes.
Not Ideal for Renovations
Prefab works best for new construction rather than renovations or additions. Retrofitting prefab sections onto an existing structure requires extensive customization and can negate many of the prefab benefits.
Site Constraints
While prefab offers minimal site disturbance, the lot does need to be accessible by road for the units to be delivered. Installation also requires a clear route from the street to the foundation. Lots with accessibility issues may not work well for prefab.
Foundation Requirements
Prefab homes need reinforced foundations designed to specification to securely bolt the units. Foundation costs may be higher than a typical build. Some sites with soil conditions unsuited to reinforced slabs may not work for prefab.
Resale Value Concerns
There is a perception that prefab homes may not appreciate as well as traditional homes. However, data shows that prefabs appreciate comparably if they are well-built. Nonetheless, appraisers in some markets may still undervalue prefab homes.
High Transport Costs
For prefab homes, the bulk of construction takes place remotely. Then the home sections need to be trucked to the site for assembly. Long transport distances can add significant shipping costs, especially for rural sites.
Timeline Inflexibility
Once a prefab home begins production, the manufacturing timeline is difficult to speed up or slow down. The prefab timeline may not align perfectly with obtaining permits, site prep work and utility connections.
Little Cost Saving for High-end Homes
The cost benefits of prefab are most apparent for standard, mid-range homes. For high-end luxury prefabs with extensive customization, costs may approach conventional homes.
In summary, considerations like limited customization, design restrictions, size constraints, site suitability and transport logistics should be taken into account when weighing using prefab construction. For the right home buyer, prefab cons may be outweighed by the many pros and efficiencies.
Are prefabricated homes cheaper than traditional construction?
Prefabricated homes tend to have lower construction costs compared to traditional stick-built homes, but there are some caveats. Here is an overview of prefab home pricing and how it compares:
Prefab Home Cost Factors
The cost of a prefab home depends on several factors:
- Size – The total square footage and number of floors/levels
- Customization – The extent of design customization vs standard models
- Features and Finishes – Quality of cabinetry, flooring, appliances etc chosen
- Foundation – Type of foundation required based on location
- Delivery – Distance from factory to site which impacts shipping
- Assembly – On-site labour needed for installation and finishing
More customization and higher-end finishes will increase the budget, while smaller standard models help reduce costs.
Prefab Cost Savings
Prefab homes can cost 10-20% less compared to traditional on-site construction. Here are some of the factors that lead to savings:
- Factory workflow and machinery increase efficiency and reduce waste
- Bulk purchasing of materials brings down costs
- Less manual labor required overall
- Shorter construction timeline reduces finance costs
- Lower risk of weather damage and re-work
Exact cost differences depend on the prefab company, model, location and other specifics.
Traditional Home Cost Factors
For traditional stick-built homes, the main cost drivers are:
- Materials – Lumber, bricks, roofing, fixtures selected
- Labor – Hourly rates and total hours for subcontractors
- Duration – Longer timelines mean higher financing costs
- Land Acquisition – Budget will be higher for prime lots
- Customization – More unique designs and finishes raise costs
- Foundation – Particularly excavation needs in difficult terrain
Higher-end custom homes with premium materials and features will fall in the upper cost range.
Cost Comparison Table
Here is an approximate comparison of costs for a 2,500 sq.ft single family home:
Cost Factor | Prefabricated | Traditional |
---|---|---|
Materials | $100,000 | $150,000 |
Labor | $50,000 | $100,000 |
Timeline | 5 months | 10 months |
Financing | $10,000 | $20,000 |
Total Cost | $160,000 | $270,000 |
As the table shows, prefab homes can cost over $100,000 less for an equivalent size and features. The ability to assemble the home much faster onsite is a major cost factor.
When Prefab Loses Cost Advantage
However, prefab homes can end up costing similar or more than traditional homes in certain scenarios:
- Highly customized prefab homes
- Luxury, high-end finishes prefab homes
- Larger homes over 3,500 sq.ft.
- Sites located very far from prefab factory
The cost advantage is strongest for standardized mid-range prefab homes under 3,000 sq.ft.
In summary, prefabricated homes do provide significant construction cost savings in most cases thanks to the efficiencies of offsite manufacturing. But for certain high-end applications, the pricing difference may be negligible. Always get multiple bids before deciding.
How long does it take to build a prefab home?
One of the biggest advantages of prefabricated construction is the faster timeline compared to traditional on-site building. Here is an overview of how long it takes to build a prefab home:
Prefab Construction Timeline
The typical timeline to build a prefab home is:
- 2-6 weeks for design, budgeting, permitting and financing
- 4-6 weeks for factory construction of modules
- 1-2 weeks for foundation work onsite
- 1-3 days for trucking prefab sections to site
- 1-2 weeks for onsite assembly and finishing
In total, a move-in ready prefab home can be completed in just 4-6 months on average.
Here is a sample prefab construction schedule:
Phase | Duration |
---|---|
Design, approvals, financing | 4 weeks |
Factory fabrication | 6 weeks |
Foundation pouring | 2 weeks |
Modules delivery | 2 days |
Onsite assembly | 1.5 weeks |
Finishing (interior, exterior) | 3 weeks |
Total Time | 5 months |
Some factors that can influence the timeline:
- Size of home – Larger homes take longer
- Customization – More complex designs add time
- Site accessibility – Impacts delivery and assembly
- Permitting – Some areas have longer approval times
Traditional Building Timeline
For traditional stick-built onsite construction, the typical timeline is:
- 4-8 weeks for design, budgeting, permitting and financing
- 2-4 weeks for site preparation and foundation
- 4-6 months for frame construction and roofing
- 2-3 months for exterior finishing (siding, windows, doors)
- 2-3 months for interior finishing (drywall, paint, trim, fixtures)
- 1-2 months for inspections, utilities, landscaping
In total, construction usually takes 9-12 months. Larger or customized homes can take over a year to complete.
Phase | Duration |
---|---|
Design, approvals, financing | 6 weeks |
Foundation and site prep | 4 weeks |
Framing and roofing | 5 months |
Exterior finishing | 3 months |
Interior finishing | 2.5 months |
Inspections and landscaping | 6 weeks |
Total Time | 12 months |
Key factors impacting traditional build timelines:
- Number of change orders and rework needed
- Any weather delays or shutdowns
- Speed of material deliveries
- Crew and trade contractor availability
Timeline Comparison
Based on typical timeframes, prefabricated homes are completed 50-60% faster than traditional construction. For instance:
- A prefab home taking 5 months would take 10-12 months using traditional building
- A 10 month traditional build could be a 4-5 month prefab project
This significant time savings is possible because up to 80% of construction is done in the controlled factory environment. Onsite work is minimized.
In summary, prefabricated homes provide a much faster path to move-in ready completion, usually in less than half the time of standard construction. The accelerated schedule is a major benefit for buyers eager to settle into their new home.
Are prefabricated homes customizable?
Prefabricated homes are often associated with cookie-cutter designs, but many customization options are available depending on the manufacturer. Here is an overview of customization possibilities for prefab homes:
Floor Plan Options
Most prefab builders offer multiple standard floor plans to choose from, ranging from compact 1-2 bedroom designs to spacious 5+ bedroom layouts. While layouts cannot be completely customized, buyers can select the plan that best fits their space needs.
Some builders also allow modifications like:
- Adding or removing interior walls/doors
- Flipping the layout or reversing it
- Adjusting room and space dimensions
Within structural limitations, layouts can be adapted to suit buyer preferences.
Exterior Looks
Prefab home exteriors can be customized with different material finishes:
- Siding – e.g. wood, metal, brick, stone
- Windows – sizes, grid patterns, trim
- Entry doors – styles, colors, sidelights/transoms
- Roofing – shingles, standing seam metal, flat roof
- Garages – attached or detached
This allows buyers to personalize the home’s aesthetic and street appeal.
Interior Finishes
Interior finishes and features allow for plenty of personalization:
- Flooring – hardwood, tile, laminate, vinyl, carpet
- Cabinetry – shaker, modern, color choices
- Countertops – granite, quartz, butcher block
- Bath fixtures – sinks, tubs, showers, vanities
- Appliances – brands, styles, pro-grade options
- Smart home systems – lighting, climate, security
Finish selection is where most prefab customization takes place.
Custom Add-Ons
Additional options allow further customization:
–Bonus spaces – detached garages, she sheds, guest suites
–Outdoor features – decks, pergolas, spas, outdoor kitchens
–Home systems – solar panels, backup generators, EV chargers
–Accessibility features – wheelchair ramps, lifts, roll-in showers
While not built offsite, these can be incorporated during final onsite assembly.
Design Services
Most prefab builders have in-house designers to help customize within their available options, including:
- Collaborating on floor plan and layout preferences
- Modeling different exterior finish combinations
- Selecting cabinetry, lighting and other interior features
- Visualizing final design with 3D walkthroughs
This guidance helps buyers personalize plans while keeping options within feasible parameters.
Cost of Customization
More customization does add to the final price:
- Floor plan changes add ~5-15%
- Exterior finish upgrades add ~10-20%
- Interior design selections add ~20-30%
- Bonus structures and add-ons add ~15-40%
But the convenience of having it all done by the same company can outweigh added costs.
In summary, while not as customizable as on-site construction, prefab homes offer ample options to tailor layouts, aesthetics, finishes and features to your taste within the inherent structural constraints. Expert design help is available. Added customization does impact the overall budget.
Do prefab homes appreciate in value like traditional homes?
Whether prefabricated homes gain value over time similar to traditional site-built homes is a common question for buyers considering prefab construction. Here are some key considerations around prefab home appreciation:
Factors Impacting Home Value
All homes appreciate based on broader housing market conditions like:
- Location desirability
- Local real estate trends
- Interest rates and lending environment
- Demographic demand shifts
- Overall home inventory supply
Beyond location, individual home features that affect value include:
- Square footage
- Bedroom and bathroom count
- Layout and functionality
- Quality of construction
- Curb appeal and condition
- Finishes and amenities
- Energy efficiency
- Property features like lot size
These factors account for over 80% of a home’s value regardless of construction method.
Prefab vs Site-Built Appreciation
Several studies have looked at appreciation trends specifically for prefab homes compared to traditional homes. Key findings:
- According to Attom Data, prefab homes appreciated nationwide by 12% annually from 2010-2018.
- This matches the 11-12% annual range for site-built homes over the same period.
- Appreciation rates vary by region but prefab and traditional are comparable.
- In high growth areas like Austin, Portland and Seattle, prefab home values increased multi-fold.
So properly designed and built prefab homes gain value similarly to stick-built homes in most markets.
Reasons for Lower Prefab Value Perceptions
However, prefab homes may be undervalued in appraisals for a few reasons:
- Appraiser bias favoring conventional building methods
- Lack of good prefab sale comps in some areas
- Depreciation for modular/mobile homes affecting perceptions
- Newer niche market with future resale data still developing
But genuine market data shows prefab appreciation rates at par with site-built homes. Buyers should look at direct comps rather than rely on perceptions.
Maintaining Value Over Time
For long-term sustained value, prefab homes must be:
- Of high quality construction, materials and design
- Well-maintained over time – both home and landscaping
- Competitive in size and features for the neighborhood
- Professionally appraised using valid prefab comparables
Closing any potential site-built vs prefab appreciation gap depends on educating appraisers as the market matures.
In summary, location dominates value while individual property features matter more than construction method. Despite outdated biases, data shows prefab homes appreciate comparably to traditional homes in most markets when all other factors are equal.
Are prefabricated homes energy efficient?
Prefabricated homes are designed with energy efficiency in mind through their construction methods, materials used, and design features. Here are some of the ways prefab homes achieve high energy performance:
Tight Construction
Prefab homes are built with precise dimensions and minimal air leakage since construction occurs in a quality-controlled factory setting. This results in a tighter building envelope compared to traditional field construction.
Key energy-saving factors:
- Wall panels with integrated insulation minimizes thermal bridging
- Advanced sealing techniques reduce air infiltration
- High performance windows and doors limit heat transfer
- Fewer gaps, joints, seams for air leaks versus field construction
This precision translates into reduced heat loss and lower energy consumption.
High Insulation
Prefab building components use the latest insulation materials and installation methods:
- Walls – Integrated rigid foam insulation rated R-20 to R-40+
- Roof – Spray foam, rigid foam or fiberglass batt insulation, R-50+
- Floor – Foam or rigid board insulation under floor decking
- Minimal thermal breaks compared to stud framing
By encapsulating the entire home in insulation, prefab homes require less energy to heat and cool.
Efficient HVAC Systems
Prefab homes are designed with right-sized and energy-efficient HVAC systems:
- High SEER rating air conditioners (SEER 16+)
- Ductless mini-split heat pumps for zone control
- High efficiency furnaces (96% AFUE+)
- Smart thermostats and controls
- HVAC commissioning for optimal airflow and performance
Properly designed systems keep prefab homes comfortable while using the minimum energy.
High Performance Materials
Prefab builders use advanced building materials to raise efficiency:
- Structural insulated panels (SIPS) made of foam between oriented strand board (OSB) have high insulation values
- Insulated concrete forms (ICFs) use foam forms that remain as thermal mass
- Energy trusses integrate insulation to eliminate thermal breaks
- Low-E windows and doors reduce heat transfer
These engineered materials make the home envelope intrinsically energy-efficient.
Solar Power
Many prefab builders offer solar PV systems as an upgrade or even integrate it standard into homes. Features may include:
- Roof-mounted solar panels and microinverters
- Battery storage for backup power and grid independence
- EV chargers to use solar energy for electric vehicles
- Smart energy monitoring systems
Solar options enable prefab homes to generate much of their own electricity.
Passive Solar Design
Prefab floor plans optimize passive solar through:
- Elongated east-west axis to maximize southern exposure
- Strategic window placement for solar gain in winter, shading in summer
- Open layouts that facilitate airflow and cross-ventilation
- Overhangs that block summer sun but allow winter sun
- Thermal mass materials like concrete floors that absorb heat
Smart solar orientation reduces the need for mechanical heating and cooling.
In summary, thanks to tight construction, ample insulation, efficient equipment, advanced materials and solar design, prefabricated homes can achieve exemplary energy performance meeting net zero or Passive House standards.
How durable and long-lasting are prefab homes compared to traditional homes?
A common perception of prefabricated (prefab) homes is that they are less durable than traditional stick-built homes. However, prefabs can actually match or exceed standard construction in longevity when built properly. Here is how prefab durability compares:
Structural Durability
Prefab homes use steel, timber, or concrete structural systems that are durable and robust:
- Steel framing resists rot, termites, mold and is non-combustible. Properly maintained, it lasts 50+ years.
- Wood framing made of engineered I-beams or LVL lumber avoids flaws of dimensional lumber and lasts over 30 years.
- Concrete used in some prefab wall systems or as floor slabs is rot/mold-proof and extremely long-lasting.
Structural materials are weather and decay-resistant and designed for multi-decade life.
Resilient Building Envelope
The insulated exterior shell of prefab components is durable:
- sip sheathing made of rigid foam between OSB creates air/water barrier
- Metal siding options resist gusts up to 150+ mph winds
- Fiber cement siding lasts 50+ years
- Advanced caulking/sealing prevents water intrusion
- Minimal fasteners compared to stick framing reduces leakage points
A tightly constructed envelope prevents moisture issues that impact longevity.
Controlled Construction
Building in a factory allows consistent quality control unfeasible on construction sites:
- Precisely cut materials using CNC machines
- Consistent sealing/caulking installation
- Careful inspection at each production step
- Protection from weather/elemant damage during construction
Controlled indoor assembly results in durable and flawless finished components.
Moisture Management
Prefab homes incorporate effective moisture control strategies:
- Vapor retarders, air barriers in wall/floor assemblies
- Rain screening behind exterior finishes allows drainage
- Overhangs and proper flashing prevent water entry
- Mold/mildew resistant materials like metal framing
Keeping components dry durably prevents structural issues from moisture.
Foundation Options
Prefabs use various durable foundation systems:
- Monolithic slabs able to withstand freeze-thaw and soil movement
- Concrete block or poured walls for basements/walkouts
- Galvanized steel/concrete piers stable for decades
Engineered foundations designed for prefab load requirements provide long-term stability.
Less On-Site Exposure
Minimal time spent on an active construction site reduces risks:
- Shorter weather/element exposure during build
- Less handling of materials resulting in dents/cracks
- Reduced theft or vandalism of unfinished building components
- Avoids improperly stored materials degrading prematurely
The accelerated prefab timeline preserves durability.
In summary, using robust materials, factory build quality, moisture control and resilient foundations, prefabricated homes offer comparable or superior longevity versus traditional site-built homes.
What maintenance is required for prefabricated homes?
Prefabricated homes have some unique maintenance requirements compared to site-built homes. Here are the key areas that require periodic attention to keep a prefab home looking its best and functioning optimally:
Structure and Envelope
- Inspect exterior sealants, adhesives every 2-3 years and reseal gaps as needed to prevent air or water leaks. Pay attention to window and door frames.
- Check for any signs of damage on exterior finishes like dents on siding. Spot repair and touch up paint annually.
- Examine roofing for debris buildup, damaged shingles/flashing and clear drains/gutters. Have a professional inspect annually.
- For crawl space foundations, inspect vapor barriers for any rips and engage pest control for termite/rodent prevention.
Mechanical Systems
- HVAC equipment should be serviced annually by a technician – check refrigerant levels, condensate drains, blower motors. Replace filters every 3 months.
- Inspect plumbing pipes and supply lines for leaks or corrosion every year.Flush sediment from tankless water heaters.
- For homes with septic systems, pump septic tanks every 3-5 years and avoid pouring harsh chemicals down drains.
- Test smoke, CO2 and security alarms monthly, replace batteries every 6 months to keep operational.
Interior Finishes
- Inspect cabinet hinges/drawer glides, tighten or replace any loose hardware as needed
- Re-caulk showers, tubs and sinks annually using a mildew resistant silicone. Ensure proper drainage.
- For engineered wood flooring, refinish scratches as needed and clean using approved cleaners only.
- Windows may need re-sealing over time. Clean tracks and lubricate to ensure smooth operation.
Site/Landscaping
- Pressure wash exterior siding every 2-3 years to maintain appearance.
- Re-stain wooden decks/fences every 2-4 years after cleaning and prepping surfaces.
- Prune trees/shrubs away from the home exterior and clear gutters.
- Maintain graded drainage around home to prevent water pooling against foundation.
Long-Term Maintenance
- Budget for roof replacement every 20-25 years.
- Plan for exterior paint refresh every 8-10 years.
- HVAC equipment typically lasts 10-15 years before replacement.
- Water heaters need replacement after 8-12 years.
- Inspect foundation for settling/cracks and re-level home as needed.
Following recommended maintenance schedules for prefab homes preserves structural integrity, functionality and aesthetics for the long term.
What are the different types of prefabricated homes?
There are several distinct construction methods used in building prefabricated homes, each with their own characteristics and benefits. The main types of prefab homes include:
Modular Homes
Modular homes are built with multiple box-shaped modules transported to site and joined together. Key features:
- Modules are typically 12 to 16 feet wide and up to 60 feet long
- Can be single or multi-story
- Transported on trucks and craned onto foundation
- More customizable than other prefab types
- Accounts for ~75% of prefab market
Modular components with open layouts and modern finishes are common in suburban subdivisions.
Panelized Homes
Panelized prefabs use large flat wall, floor and roof panels assembled onsite. Features include:
- Wall panels up to 8 feet wide by 24 feet high
- Floors and roof in ~4 feet by 8 feet assemblies
- Panels joined using screws, sealant, lumber
- Very quick onsite assembly
- Well-suited for remote or urban infill sites
Panels combine speed of prefab with flexibility of site-built.
Tiny Homes
Tiny prefabs under 400 sq.ft use modular or panelized systems to maximize small spaces:
- Compact footprint for affordability and mobility
- Sleeping lofts, Murphy beds, convertible furniture
- Efficient kitchenettes and bathrooms
- Towable by truck for recreational or ADU uses
Tiny homes simplify living and housing costs.
Shipping Container Homes
These unique prefabs repurpose used shipping containers:
- Containers typically 8 feet wide by 20/40 feet long
- Stacked or joined horizontally into modules
- Insulated and finished as inhabitable spaces
- Edgy, modern industrial aesthetic
- Lower cost than other prefab types
Shipping containers create funky, eco-friendly homes.
Hybrid Homes
A hybrid combines prefab components like panels or boxes with traditional stick-built framing for a customized design.
- Mix of offsite prefab and onsite construction
- Used to integrate a prefab addition onto an existing home
- Allows prefab efficiencies along with maximal customization
Hybrid homes provide the best of both building worlds.
In summary, major prefab types include modules, panels, tiny homes, containers, and hybrids. Buyers can choose an approach aligned with their priorities like cost, customization, or structural needs.
Key Takeaways
- Prefabricated homes provide faster construction thanks to mass manufacturing components offsite. They can be built in 4-6 months vs 9-12 months for traditional homes.
- Prefabs cost 10-20% less on average than comparable site-built homes due to improved efficiency and less waste.
- Highly controlled factory conditions allow superior quality control for prefabricated homes.
- While not as customizable as on-site building, prefabs offer ample options for finishes, layouts, and features.
- Thanks to tight construction and integrated efficiency measures, prefab homes are highly energy efficient.
- Prefab structural materials like steel, concrete and engineered wood make them just as durable as traditional homes.
- Regular maintenance for the building envelope, roof, electrical, plumbing and HVAC keeps prefabs like new.
- Main prefab types are modular boxes, wall/roof panels, tiny homes, shipping containers and hybrid designs.
In Conclusion
- With advantages like faster build time, lower costs, and resilience, prefabricated homes are a smart choice for many buyers and suitable sites.
- Drawbacks to weigh include limited customization, onsite constraints, and potential resale bias in some markets.
- New technologies and efficiencies help prefab homes match or exceed traditional building in quality, features and longevity.
- For an affordable, quality home with minimal fuss, prefabrication offers a compelling and viable modern construction method worth exploring.
kontraktor rumah
bina rumah
pinjaman lppsa
pengeluaran kwsp
spesifikasi rumah
pelan rumah
rekabentuk rumah
bina rumah atas tanah sendiri
kontraktor rumah selangor