- Bina Rumah Batu-Bata
- Zero Deposit
- Spesifikasi Rumah
- Lokasi Projek
- Pembiayaan LPPSA
- Garis Panduan LPPSA (Rasmi)
- Soalan Lazim LPPSA
- E-Book LPPSA (Download)
- 1. Apa itu LPPSA?
- 2. Kelebihan LPPSA
- 3. Syarat Kelayakan
- 4. Jenis-Jenis Pembiayaan
- Jenis 1 – Pembelian Rumah Kediaman Yang Telah Siap
- Jenis 2 – Membina Rumah Di Atas Tanah Sendiri
- Jenis 3 – Membeli Rumah Kediaman Yang Sedang Dibina
- Jenis 4 – Pembelian Tanah Bagi Pembinaan Rumah
- Jenis 5 – Melunaskan Keseluruhan/ Sebahagian Pinjaman Sedia Ada Daripada Bank/ Institusi Kewangan
- Jenis 6 – Pembinaan Rumah Kediaman Di Atas Tanah Yang Sedang Dibiayai Oleh BPP/ LPPSA
- Jenis 7 – Ubah Suai Rumah Yang Sedang Atau Telah Selesai Bayar Melalui LPPSA
- 5. Semak Kelayakan LPPSA
- 6. Dokumen Yang Diperlukan
- 7. Insurans/ Takaful LPPSA
- 8. Kos Yuran Guaman
- 9. BONUS: Bina Rumah
- Pembiayaan Koperasi
- Pengeluaran KWSP
- Bayaran Tunai
- Kalkulator
IBS Construction in Malaysia: Revolutionizing the Building Industry
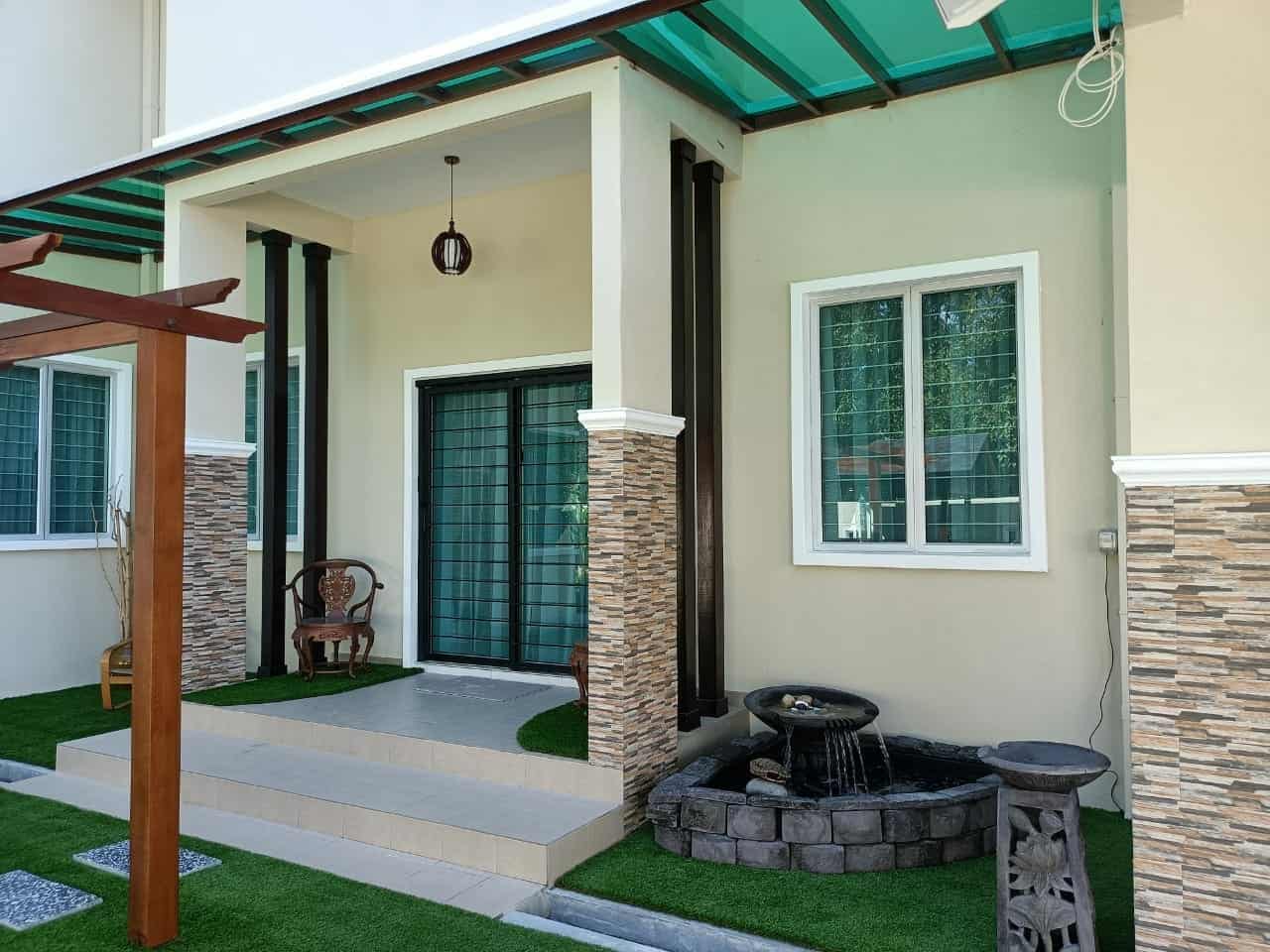
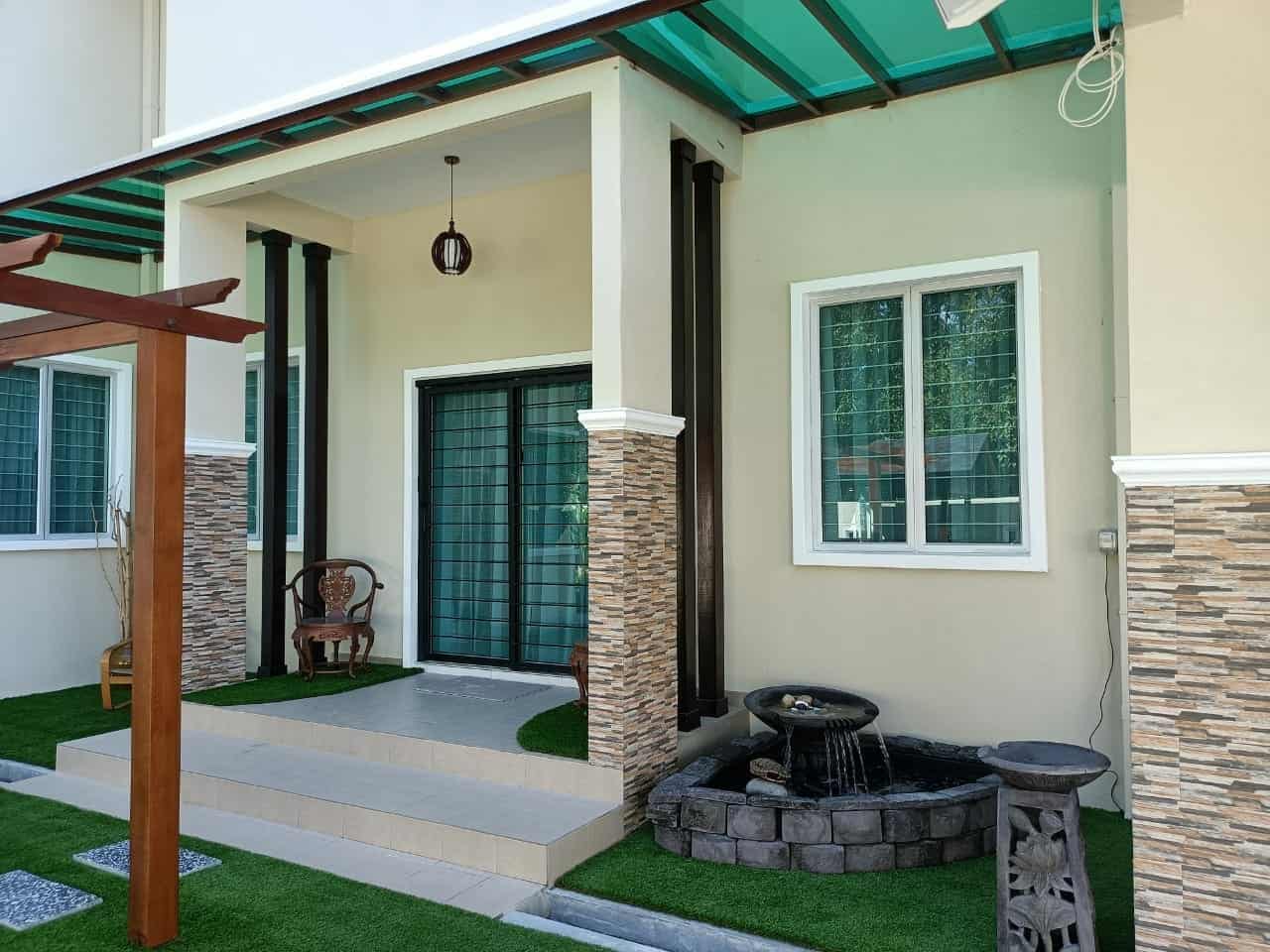
IBS Construction in Malaysia: Revolutionizing the Building Industry
Table of Contents
- Introduction: Embracing Innovation in Construction
- What is IBS Construction?
- Advantages of IBS Construction
- Faster Construction Time
- Cost Efficiency
- Improved Quality and Safety
- Environmentally Friendly
- Types of IBS Construction Systems
- Precast Concrete Systems
- Steel Framing Systems
- Timber Systems
- Modular Systems
- IBS Implementation in Malaysia
- Government Initiatives and Support
- IBS Roadmap
- Projects Showcasing IBS Success
- Challenges and Limitations of IBS Construction
- Lack of Awareness and Understanding
- Skilled Workforce and Training
- Standardization and Compatibility Issues
- Initial Investment Costs
- Overcoming Challenges and Promoting IBS Adoption
- Awareness Campaigns and Education
- Collaboration and Knowledge Sharing
- Incentives and Grants
- Research and Development
- Conclusion
- FAQs
- What does IBS stand for?
- How does IBS construction reduce construction time?
- Is IBS construction more expensive than traditional methods?
- Can IBS construction be applied to all types of buildings?
- How can the government encourage IBS adoption?
Introduction: Embracing Innovation in Construction
The construction industry in Malaysia is undergoing a significant transformation with the introduction of Industrialized Building Systems (IBS). IBS construction is revolutionizing the way buildings are constructed by incorporating off-site manufacturing, standardization, and mechanization. This article explores the concept of IBS construction, its advantages, implementation in Malaysia, challenges, and strategies to promote its adoption.
What is IBS Construction?
IBS construction refers to the utilization of standardized and pre-manufactured components in the construction process. These components, such as precast concrete panels, steel frames, or modular units, are manufactured in a controlled factory environment before being transported to the construction site for assembly. The adoption of IBS methods reduces reliance on traditional brick-and-mortar construction and introduces a more systematic and efficient approach.
Advantages of IBS Construction
Faster Construction Time
One of the key advantages of IBS construction is its ability to significantly reduce construction time. With the majority of components prefabricated off-site, construction activities can be carried out simultaneously, leading to shorter project durations. IBS also minimizes weather-related delays, allowing construction to proceed in a controlled environment.
In traditional construction methods, various activities such as foundation work, structural framing, and finishing processes are carried out sequentially. This sequential approach often leads to project delays, as one process cannot start until the previous one is completed. IBS construction, on the other hand, enables different construction activities to be carried out simultaneously, greatly accelerating the construction timeline.
Cost Efficiency
Despite the initial investment required for setting up IBS facilities, the long-term cost savings outweigh the upfront expenses. The streamlined construction process reduces labor requirements, minimizes material wastage, and lowers the overall project duration. Additionally, the improved quality and reduced maintenance needs of IBS buildings result in cost savings over their lifecycle.
In traditional construction, labor costs constitute a significant portion of the overall project expenses. With IBS construction, the reliance on on-site labor is significantly reduced. The majority of construction activities, such as component manufacturing and assembly, are shifted to controlled factory environments. This shift allows for efficient use of labor resources and minimizes the need for on-site construction workers. As a result, labor costs are reduced, leading to overall cost savings in IBS projects.
Furthermore, IBS construction minimizes material wastage through precise manufacturing processes. Components are manufactured to exact specifications, reducing the need for on-site modifications and material trimming. The controlled factory environment also enables better inventory management, optimizing material usage and minimizing waste. These factors contribute to cost efficiency in IBS construction.
Improved Quality and Safety
IBS construction ensures a higher level of quality control compared to traditional construction methods. The factory environment enables precise manufacturing and rigorous quality checks, leading to consistent and reliable building components. The standardized nature of IBS components also eliminates variations in quality that can occur with on-site construction.
Additionally, the use of standardized components in IBS construction enhances construction safety. The off-site manufacturing of components reduces on-site risks and accidents associated with traditional construction methods. Workers are exposed to a controlled environment with better safety measures in place, minimizing the chances of on-site injuries.
The improved quality and safety of IBS construction have significant implications for building durability and occupant satisfaction. IBS buildings exhibit better structural integrity and are less prone to defects and maintenance issues. The use of high-quality components and standardized construction practices ensures that buildings meet stringent quality standards, providing long-term benefits to owners and occupants.
Environmentally Friendly
With sustainability becoming a priority, IBS construction aligns with eco-friendly practices. The manufacturing process of IBS components generates less waste, as materials can be recycled and reused. Additionally, the controlled construction environment minimizes pollution and noise disturbances, resulting in a reduced environmental footprint.
IBS construction promotes resource efficiency through optimized material usage. Precise manufacturing processes ensure minimal material wastage, reducing the demand for raw materials. Moreover, IBS components are designed for easy disassembly and reusability, enabling future building modifications or deconstruction without significant environmental impact.
The controlled factory environment in IBS construction also minimizes pollution and noise pollution. Construction activities that traditionally generate dust, noise, and emissions are shifted away from the construction site, reducing the impact on the surrounding environment and communities.
Types of IBS Construction Systems
IBS construction encompasses various systems that utilize pre-manufactured components. The following are some of the commonly used IBS construction systems:
Precast Concrete Systems
Precast concrete systems involve the production of concrete components, such as walls, slabs, and columns, off-site. These components are then transported to the construction site and assembled using various joining techniques. Precast concrete systems offer versatility, durability, and excellent fire resistance.
Precast concrete components are manufactured in controlled factory environments under strict quality control measures. They are designed to meet specific project requirements and can be customized to achieve desired architectural aesthetics. The use of precast concrete in IBS construction allows for faster construction and improved quality due to the standardized manufacturing processes.
Steel Framing Systems
Steel framing systems utilize steel components manufactured off-site and assembled on-site. The lightweight nature of steel makes it an ideal choice for high-rise buildings. Steel framing systems offer excellent structural integrity, flexibility in design, and resistance to pests and moisture.
Steel components in IBS construction are fabricated off-site using computer-controlled machinery. The precise manufacturing process ensures accurate dimensions and high-quality components. Steel framing systems provide design flexibility, allowing for various architectural styles and building configurations. The speed of construction is significantly increased with steel framing systems, as components can be quickly assembled on-site.
Timber Systems
Timber systems involve the use of engineered wood products, such as laminated timber or cross-laminated timber (CLT). These pre-manufactured timber components are assembled on-site, offering sustainability, aesthetic appeal, and faster construction time for low to mid-rise buildings.
Timber systems in IBS construction utilize wood products that are sustainably sourced and manufactured. The timber components are fabricated off-site, ensuring precise dimensions and structural integrity. Timber systems offer environmental benefits due to the renewable nature of wood and its carbon sequestration properties. The lightweight nature of timber components also contributes to faster and more efficient construction.
Modular Systems
Modular systems consist of factory-produced modules or units that are assembled to create a complete building. These modules can be customized according to specific design requirements and offer flexibility, portability, and reduced on-site labor needs. Modular construction is commonly used for residential and commercial projects.
Modular construction in IBS involves the production of fully finished modules in controlled factory environments. These modules can include complete rooms or sections of buildings, such as bathrooms or kitchen units. The modules are then transported to the construction site and assembled, reducing on-site construction time and labor requirements. Modular systems offer advantages in terms of quality control, construction speed, and the ability to relocate or reconfigure buildings.
IBS Implementation in Malaysia
Malaysia has been at the forefront of promoting IBS construction within the region. The government has implemented various initiatives and policies to drive the adoption of IBS methods across the construction industry.
Government Initiatives and Support
The Construction Industry Development Board (CIDB) plays a crucial role in promoting IBS construction. The CIDB provides training programs, financial incentives, and research and development grants to encourage industry players to embrace IBS. Additionally, the government mandates the use of IBS for public sector projects to further accelerate its implementation.
The CIDB collaborates with industry stakeholders to develop guidelines, standards, and certification schemes for IBS construction. These initiatives aim to create a conducive environment for IBS adoption and ensure consistent quality across projects.
IBS Roadmap
The IBS Roadmap outlines the strategies, targets, and key actions needed to promote the widespread adoption of IBS in Malaysia. It focuses on areas such as capacity building, research and development, standardization, and certification. The roadmap aims to transform the construction industry through collaborative efforts between the government, industry players, and academia.
The IBS Roadmap provides a comprehensive framework for IBS implementation, covering aspects such as capacity building through training and education, research and development for innovation, and the establishment of industry-wide standards and certification. The roadmap serves as a guide for industry players and helps align efforts towards achieving the vision of a sustainable and efficient construction sector.
Projects Showcasing IBS Success
Numerous successful projects in Malaysia highlight the advantages of IBS construction. The Kuala Lumpur International Airport 2 (KLIA2), for example, utilized precast concrete components to expedite construction and meet tight deadlines. The use of IBS methods in KLIA2 resulted in significant time savings, improved quality, and cost efficiency.
KLIA2, a major airport terminal, required rapid construction to meet the increasing demand for air travel. The adoption of precast concrete components in the construction process enabled faster assembly and reduced on-site labor requirements. The use of IBS methods allowed KLIA2 to be completed within the specified timeframe while maintaining high-quality standards.
These successful projects serve as benchmarks for the industry, demonstrating the potential of IBS construction to achieve cost and time savings without compromising on quality and safety.
Challenges and Limitations of IBS Construction
While IBS construction offers numerous benefits, there are challenges and limitations that hinder its widespread adoption.
Lack of Awareness and Understanding
Many industry players, including developers, architects, and contractors, have limited knowledge and awareness of IBS construction. The lack of understanding about the benefits and technical aspects of IBS hampers its acceptance and implementation.
Addressing the lack of awareness requires comprehensive education and information dissemination. Industry stakeholders need to be made aware of the advantages of IBS construction and its potential to transform the industry. Awareness campaigns, seminars, and workshops can play a crucial role in promoting understanding and knowledge sharing.
Skilled Workforce and Training
IBS construction requires a skilled workforce proficient in specialized manufacturing and assembly techniques. Currently, there is a shortage of adequately trained personnel in the construction industry. Enhancing training programs and developing vocational courses are necessary to address this issue.
Investments in training and education are essential to equip the workforce with the necessary skills and knowledge for IBS construction. Collaborations between industry players, educational institutions, and training centers can facilitate the development of comprehensive training programs that cater to the specific requirements of IBS construction.
Standardization and Compatibility Issues
The standardization of IBS components and their compatibility with existing construction practices is another challenge. Establishing industry-wide standards and ensuring the compatibility of different IBS systems will promote interoperability and facilitate wider adoption.
Standardization efforts should focus on harmonizing design codes, manufacturing practices, and construction processes. Collaboration between industry players, regulatory bodies, and standard-setting organizations is crucial to achieve standardized practices and ensure the compatibility of IBS components.
Initial Investment Costs
The initial investment costs associated with setting up IBS facilities and acquiring specialized equipment can be a barrier for some industry players. Financial incentives and grants can help offset these costs and incentivize businesses to embrace IBS.
The government can provide financial support in the form of grants, subsidies, and low-interest loans to encourage the adoption of IBS. Financial incentives can alleviate the financial burden on industry players and create a favorable environment for IBS investment.
Overcoming Challenges and Promoting IBS Adoption
To overcome the challenges and promote IBS adoption, several strategies can be employed:
Awareness Campaigns and Education
Conducting awareness campaigns, seminars, and workshops can educate industry stakeholders about the benefits and technical aspects of IBS construction. Sharing success stories and case studies can further highlight the positive impact of IBS.
Collaboration between industry associations, government agencies, and educational institutions can facilitate the development of educational materials, training programs, and workshops. These initiatives should target various stakeholders, including developers, architects, engineers, contractors, and students.
Collaboration and Knowledge Sharing
Encouraging collaboration between industry players, academia, and government agencies can foster knowledge sharing and innovation. Establishing platforms for information exchange and networking will accelerate the adoption and continuous improvement of IBS methods.
Industry associations and professional bodies can play a vital role in facilitating collaboration and knowledge sharing. Regular forums, conferences, and technical workshops should be organized to encourage dialogue, collaboration, and the sharing of best practices and lessons learned.
Incentives and Grants
The government can provide financial incentives, tax breaks, and grants to incentivize businesses to invest in IBS facilities and adopt IBS practices. These incentives can help offset the initial investment barriers and promote long-term cost savings.
Financial incentives can take the form of grants for research and development, tax incentives for IBS investments, and subsidies for training and certification programs. The availability of financial support will encourage industry players to explore IBS options and make informed investment decisions.
Research and Development
Investing in research and development is crucial to advancing IBS construction techniques and developing new and improved systems. Government funding and collaboration with research institutions will drive innovation and enhance the competitiveness of the construction industry.
Research and development efforts should focus on areas such as material science, construction technology, automation, and digitalization. These initiatives will lead to the development of advanced IBS systems, improved manufacturing processes, and enhanced construction methodologies.
Conclusion
IBS construction has emerged as a game-changer in the Malaysian construction industry. Its ability to expedite construction time, reduce costs, improve quality and safety, and contribute to sustainability makes it a compelling choice for building projects. While challenges exist, concerted efforts from industry players and government support can overcome these obstacles and propel Malaysia towards a more efficient and innovative construction sector.
The widespread adoption of IBS construction will require continuous collaboration, knowledge sharing, and investment in training and education. By embracing IBS methods, Malaysia can unlock the full potential of this innovative construction approach and establish itself as a leader in the region.
FAQs
- What does IBS stand for?
- IBS stands for Industrialized Building Systems.
- How does IBS construction reduce construction time?
- IBS construction reduces construction time by utilizing off-site manufacturing and simultaneous construction activities, resulting in shorter project durations.
- Is IBS construction more expensive than traditional methods?
- While there may be initial investment costs, the long-term cost savings of IBS construction outweigh the upfront expenses due to reduced labor requirements and improved building quality.
- Can IBS construction be applied to all types of buildings?
- Yes, IBS construction can be applied to various types of buildings, including residential, commercial, and institutional structures.
- How can the government encourage IBS adoption?
- The government can encourage IBS adoption through financial incentives, research and development grants, mandatory implementation in public sector projects, and awareness campaigns to educate industry stakeholders.