- Bina Rumah Batu-Bata
- Zero Deposit
- Spesifikasi Rumah
- Lokasi Projek
- Pembiayaan LPPSA
- Garis Panduan LPPSA (Rasmi)
- Soalan Lazim LPPSA
- E-Book LPPSA (Download)
- 1. Apa itu LPPSA?
- 2. Kelebihan LPPSA
- 3. Syarat Kelayakan
- 4. Jenis-Jenis Pembiayaan
- Jenis 1 – Pembelian Rumah Kediaman Yang Telah Siap
- Jenis 2 – Membina Rumah Di Atas Tanah Sendiri
- Jenis 3 – Membeli Rumah Kediaman Yang Sedang Dibina
- Jenis 4 – Pembelian Tanah Bagi Pembinaan Rumah
- Jenis 5 – Melunaskan Keseluruhan/ Sebahagian Pinjaman Sedia Ada Daripada Bank/ Institusi Kewangan
- Jenis 6 – Pembinaan Rumah Kediaman Di Atas Tanah Yang Sedang Dibiayai Oleh BPP/ LPPSA
- Jenis 7 – Ubah Suai Rumah Yang Sedang Atau Telah Selesai Bayar Melalui LPPSA
- 5. Semak Kelayakan LPPSA
- 6. Dokumen Yang Diperlukan
- 7. Insurans/ Takaful LPPSA
- 8. Kos Yuran Guaman
- 9. BONUS: Bina Rumah
- Pembiayaan Koperasi
- Pengeluaran KWSP
- Bayaran Tunai
- Kalkulator
IBS Homes: The Affordable and Efficient Building Solution
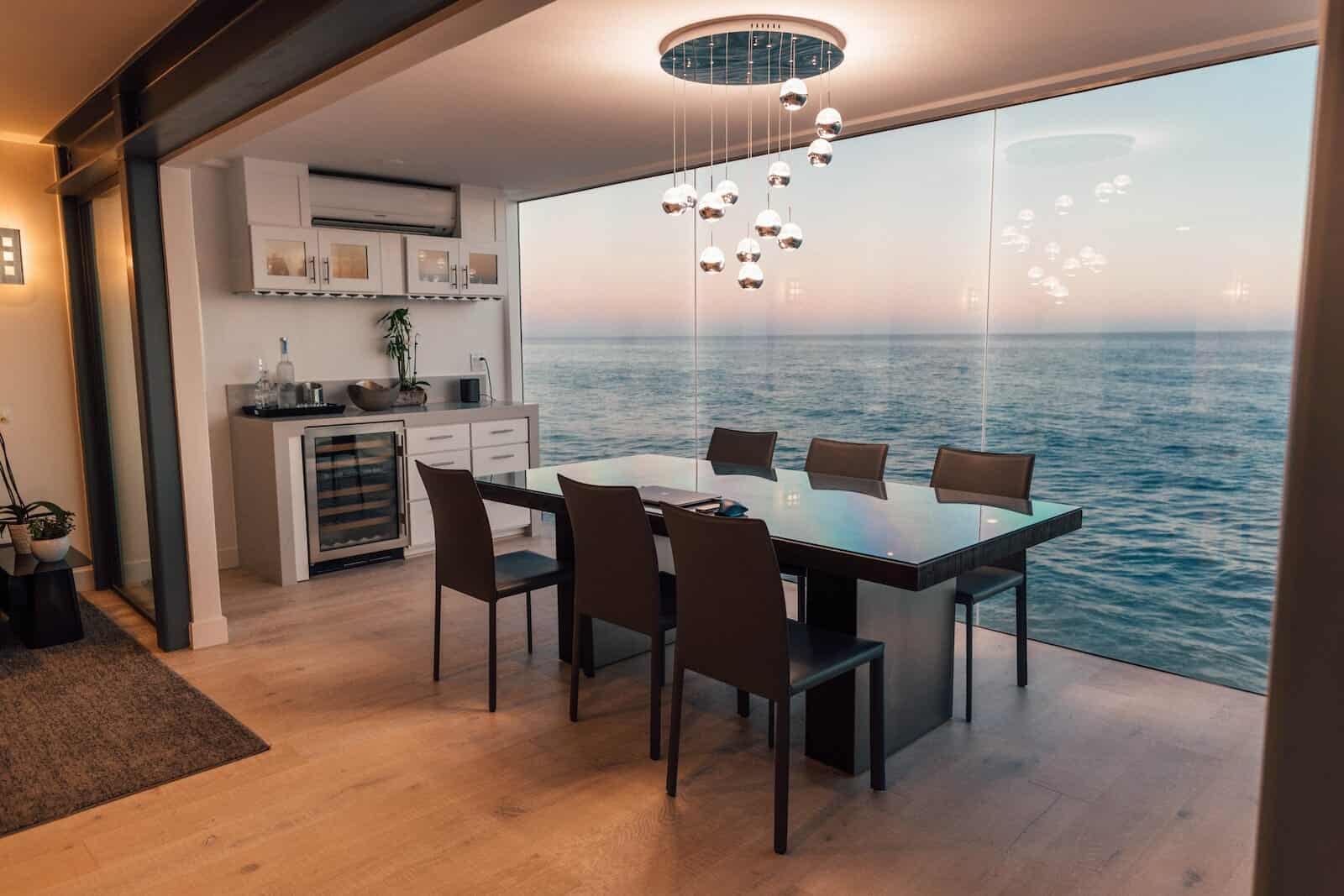
IBS Homes: The Affordable and Efficient Building Solution
- What is IBS Homes?
- How are IBS homes more affordable than traditional construction?
- What are the benefits of IBS construction?
- How are IBS homes more energy efficient?
- What materials are used in IBS construction?
- How quickly can an IBS home be constructed?
- Are IBS homes customizable or prefabricated?
- What are the limitations or drawbacks of IBS construction?
- Where are IBS homes being built right now?
- How can I learn more or get an IBS home quote?
What is IBS Homes?
IBS, or Industrialized Building System, is an innovative construction method that utilizes prefabricated components to build homes and buildings efficiently and affordably.
IBS Homes utilize prefabricated wall, floor, and roof panels that are manufactured offsite under strict quality control. These prefabricated components are then transported to the construction site and rapidly assembled to create the home’s structure.
Some key benefits of IBS construction include:
- Faster construction time – Homes can be built in as little as half the time compared to traditional construction methods. This is because up to 80% of the construction is done in a factory.
- Lower cost – Factories produce components at scale leading to reduced material and labor costs that are passed onto the homebuyer.
- Consistent quality – Factory prefabrication ensures consistent high-quality components are used for every home.
- Sustainable – Reduced construction waste, energy efficient materials, and recyclable components make IBS homes greener.
- Customizable – Homes can be customized with different layouts, finishes, facades and more to suit each client.
In summary, IBS Homes utilize offsite prefabrication and onsite assembly to construct high-quality homes faster and more affordably compared to conventional building techniques. The modular, optimized process allows for customization and sustainability as well.
How are IBS homes more affordable than traditional construction?
IBS homes can cost 10-30% less than comparable homes built using traditional construction methods. There are several key factors that contribute to the cost savings of IBS homes:
- Economies of scale – Producing components like walls, floors, and roofs in a factory allows for bulk purchasing of materials at reduced prices. This manufacturing efficiency is passed on as savings.
- Faster construction – On average IBS homes can be built in 3-5 months compared to 6-12 months for conventional homes. This significantly reduces finance costs and labor costs incurred over the construction period.
- Less waste – Prefabricated components are precision engineered to spec, minimizing material overages and construction waste. Traditional methods generate excess waste from onsite cutting and fabrication.
- Weather resistant – Factory built components can be assembled at a consistent pace regardless of weather. Poor weather often delays traditional building, increasing costs.
- Minimal customization – IBS utilizes standardized building systems which reduces per unit customization and associated costs. Custom finishes and facades can still be applied.
- Efficient logistics – Materials and components are delivered to site as needed, reducing storage costs and theft common at traditional projects.
In summary, IBS Homes are more affordable than traditional homes due to economies of scale, faster construction, less waste, weather resistance, standardization, and efficient logistics. The optimized process reduces costs by 10-30% making home ownership more accessible.
What are the benefits of IBS construction?
There are many benefits to utilizing Industrialized Building Systems (IBS) for home construction compared to conventional building methods:
- Faster construction – Homes can be completed in as little as 3-5 months, up to 50% faster than traditional techniques. This is possible as components are prefabricated offsite while foundation work begins onsite.
- Cost savings – IBS construction can reduce costs by 10-30% due to bulk material purchases, optimized fabrication, and faster completion times. This makes home ownership more accessible.
- Consistent quality – Factory built components are constructed under controlled conditions for precise engineering and finishings. This ensures consistent quality versus traditional building.
- Safer construction – Production in a controlled setting reduces safety risks inherent at a construction site. Completed components also reduce onsite cutting and fabrication work.
- Sustainable – Prefabrication generates up to 90% less waste. Components also utilize sustainable and energy efficient materials like engineered wood and recycled steel.
- Customizable – Homes can be customized with various layouts, facades, interiors, and tech integrations while utilizing standard IBS wall and roof panels.
- Resilient structures – IBS structures are highly resilient against disasters like earthquakes due to integrated wall-to-floor connections and lighter roof systems.
In summary, IBS provides faster, cheaper, safer, greener and resilient homes while still allowing for customization. It’s an innovative advancement in home building technology.
How are IBS homes more energy efficient?
IBS homes utilize several construction methods and materials that result in 15-30% better energy efficiency compared to conventionally built homes.
Here are some of the key factors that contribute to the energy efficiency of IBS homes:
- Prefabricated panels – Factory built wall, roof and floor panels result in precise sealing and insulation installation for minimal air leaks. Panels also utilize insulated cores for added efficiency.
- Improved insulation – IBS panels often feature composite insulated cores utilizing rigid foam or polyurethane insulation for high R-values and minimal thermal bridging.
- High performance windows – Energy efficient, double or triple pane windows are pre-installed in panels under climate controlled factory conditions. This enhances sealing and insulation.
- Airtight construction – Sealing between panels is done using high performance tapes and gaskets for minimal air and moisture infiltration.
- Effective HVAC – Smaller, right-sized HVAC systems can be specified as IBS homes have predictable heating/cooling loads from consistent insulation and air sealing.
- Solar integration – Solar PV arrays can be easily integrated on roof panels during manufacturing for renewable energy generation.
- Smart home tech – IBS homes can incorporate smart tech like programmable thermostats and integrated battery storage for optimal energy management.
With enhanced insulation, air tightness, solar readiness, and smart home tech, IBS homes are the future for energy efficient living.
What materials are used in IBS construction?
IBS Homes utilize innovative building materials and systems to construct high-performance, sustainable homes faster and more efficiently. Here are the key materials used:
- Structural Insulated Panels (SIPs) – SIPs feature a foam core sandwiched between wood/cement boards for insulated wall and roof panels.
- Light Gauge Steel Framing – Lightweight steel studs and trusses are used for optimized structural ribs and frames.
- Laminated Veneer Lumber (LVL) – Engineered LVL beams are used as structural supports due to strength and dimensional stability.
- Insulated Concrete Forms (ICFs) – Stackable foam forms filled with reinforced concrete create insulated foundation and floor systems.
- Automated Production Lines – Wall, floor and roof panels are fabricated using automated production lines for precision cutting, assembly and quality checks.
- Recyclable Materials – Components utilize recycled materials like scrap steel and waste wood fiber where possible to enhance sustainability.
- Energy Efficient Windows/Doors – High performance windows and doors are pre-installed in panels under climate controlled factory conditions.
- Protective Finishes – Durable waterproof coatings, sealants and concrete treatments protect components from moisture and pests during transport and assembly.
In summary, IBS utilizes the best of modern engineered materials and automated production to construct higher performing modular homes.
How quickly can an IBS home be constructed?
One of the major benefits of IBS construction is faster home building timelines, with homes able to be completed in as little as 3-5 months. Here’s an overview of typical IBS home construction schedules:
- Site preparation: 1-4 weeks. Install foundations, utilities, drainage.
- Component fabrication: 4-8 weeks. Wall, floor, roof panels prefabricated offsite.
- Onsite assembly: 1-4 weeks. Panels trucked to site and rapidly assembled.
- Interior fit-out: 4-8 weeks. Floors, cabinetry, finishes installed onsite.
- Utilities & landscaping: 1-2 weeks. Final hookups and landscaping work.
Total construction: 3-5 months.
Traditional construction typically takes 6-12 months, almost twice as long.
The accelerated schedule is possible because:
- Components like walls can be prefabricated concurrently with onsite foundation work.
- Components are finished offsite, minimizing onsite interior work needed.
- Standardized designs allow for rapid assembly versus time intensive custom construction.
- Less permitting/inspections needed as major structural work done offsite.
- Weather resistant prefabricated components unlike exposed onsite building.
IBS allows buyers to move into their new energy efficient, high quality homes faster than ever.
Are IBS homes customizable or prefabricated?
One common misconception about IBS homes is that they are purely prefabricated and lack customization. However, IBS homes can offer personalization while still utilizing standardized building systems for affordability and construction speed.
Here are some ways IBS homes can be customized to suit buyers:
- Layouts – Homes can be designed with different room configurations, sizes and layouts to match user needs and preferences.
- Facades – The exterior look can be customized by applying different finishes like stone, brick, siding. Decorative roofing and trims can also personalize the home.
- Interiors – Homeowners have flexibility on flooring materials, cabinetry, bathroom and kitchen fixtures. Paints, trim and other interior finishes are also customizable.
- Smart integrations – Features like home automation, electrified appliances, electric vehicle chargers, integrated solar and more can be incorporated.
- Landscaping – Unique landscaping options like pools, outdoor kitchens and landscape designs can help customize the home and lot.
While the structural wall, floor and roof panels are standardized for optimal cost and construction efficiency, ample personalization is still possible. Home buyers get an affordable, liveable home tailored to their lifestyle.
What are the limitations or drawbacks of IBS construction?
While IBS construction has many benefits, there are some limitations to consider:
- Higher upfront costs – IBS homes may require 10-15% more upfront payment for factory fabrication before onsite assembly. But this is recouped through lifecycle savings.
- Site constraints – Complex sites with steep slopes or poor access may be unsuitable for large panel sizes and crane requirements during assembly.
- Customization limitations – Although aesthetics and finishes can be customized, the underlying wall and roof panels use standardized sizes.
- Industry experience – The construction industry is less familiar with IBS techniques compared to traditional methods, though this is improving with more education.
- Codes & approvals – Navigating codes and approvals for factory built structures presents challenges in some regions though automated design validation helps.
- Factory logistics – Additional coordination and costs involved in transporting fabricated components from factory to site.
- Builder partnerships – Home buyers may need to partner with builders experienced in IBS construction techniques to ensure proper assembly.
However, the benefits of faster, affordable, higher-performing and more sustainable construction outweigh most limitations of IBS homes for the majority of projects. Continued IBS education and adoption is improving upon these drawbacks.
Where are IBS homes being built right now?
The market for IBS homes is expanding beyond early adopter regions as more home buyers discover the benefits:
United States
IBS home projects are on the rise in states like California, Washington, Texas and Florida. Urban infill projects have utilized IBS for fast multi-family housing.
Canada
Ontario and British Columbia lead IBS home construction, though Quebec and Alberta are growing markets.
United Kingdom
IBS single-family homes and apartments are gaining ground throughout England driven by affordability and sustainability needs.
Australia
Queensland and Victoria have massive IBS housing developments as demand surges in metro regions. IBS performs well in hot climates.
Asia Pacific
Singapore and Malaysia have extensive IBS high-rise residential projects. Japan and Thailand are also growing IBS markets.
Middle East
The UAE and Saudi Arabia are major adopters of IBS for affordable villas and multifamily structures to house growing populations.
As more regions create building codes and standards for offsite construction, adoption of IBS homes will continue accelerating across the globe. The future of home building is here.
How can I learn more or get an IBS home quote?
If you’re interested in learning more about IBS homes or getting a price quote, here are some tips:
- Research builders – Search for IBS home builders in your region online and read reviews. Reach out to builders directly to ask project portfolio questions.
- Take virtual tours – Many IBS builders offer virtual model tours so you can get a feel for the homes’ quality and finishes.
- Browse design galleries – Most builders have design galleries on their websites to view floorplans and possible customization options like facades.
- Ask about benefits – Discuss your builder’s IBS approach and ask how it provides advantages over traditional building in terms of cost, speed and energy savings.
- Clarify timeline – Understand the full construction timeline including permit approvals, site prep, factory schedule and final site assembly.
- Get itemized quotes – Request an itemized quote to understand exactly what is included and where cost savings are realized.
- Learn about warranties– Ask about structural and performance warranties that come with factory engineered IBS home components.
- Visit a site– If possible, visit an active IBS home construction site to witness the assembly process firsthand.
With some upfront research and provider comparison, you can make an informed decision if an IBS home is the right choice for your next project.
Key Takeaways
- IBS homes utilize prefabricated structural components for faster, affordable construction.
- Factory build IBS components generate up to 30% in cost savings versus traditional methods.
- Energy efficiency improves by 15-30% thanks to air tight panels and effective insulation.
- While standardized, IBS homes can be customized with layouts, facades and interiors.
- Global adoption is accelerating as more regions approve modular construction.
- Interested buyers should research experienced IBS home builders in their local area.
Conclusion
- IBS construction techniques offer major advantages over traditional building using standardized structural components.
- Home buyers benefit from lower costs, faster completion times, high energy efficiency and resilience against disasters.
- Customization of IBS homes is still possible through different layouts, finishes and tech integration.
- Growth in global IBS housing is rising as builders demonstrate the benefits to buyers.
- Homeowners interested in quality, sustainability and affordability should strongly consider IBS for their next home project.
kontraktor rumah
bina rumah
pinjaman lppsa
pengeluaran kwsp
spesifikasi rumah
pelan rumah
rekabentuk rumah
bina rumah atas tanah sendiri
kontraktor rumah selangor